Continuous basic business through digitalisation, condition monitoring and predictive maintenance
- markus923
- Jan 2, 2023
- 2 min read
Machine manufacturers can develop a continuous base business and compensate for sales valleys in the machine business with the help of digitalisation, condition monitoring and predictive maintenance. How exactly can this be achieved? A few ideas and options worth thinking about.

The investment business is currently very cyclical. Typically, equipment costs a lot of money and once it is sold, no further significant revenue can be generated with the customer. The sale of spare parts and equipment checks is very small compared to the one-off revenue generated by the sale of the equipment. This creates a very cyclical business for equipment manufacturers and a very cyclical cash flow that is difficult to plan. This situation contrasts with the need to continuously utilise trained, highly specialised personnel, e.g. designers, technicians.
Opportunity for continuous additional business
A service offer based on the combination of digitalisation, condition monitoring and predictive maintenance can compensate for the sales valleys and, above all, offer the opportunity for continuous, attractive business. These new services are not sold to customers as a one-off, but are charged at regular intervals. The challenge is to communicate the added value of these additional services to the customer, as he can also stop booking these additional services at any time. Therefore, the benefit of these services, which are financed through fees and running costs, must be recognisable and attractively communicated at all times.
The selective, targeted use of modern technologies such as artificial intelligence and ultrasound makes it possible today to successfully pass this cost-benefit calculation.
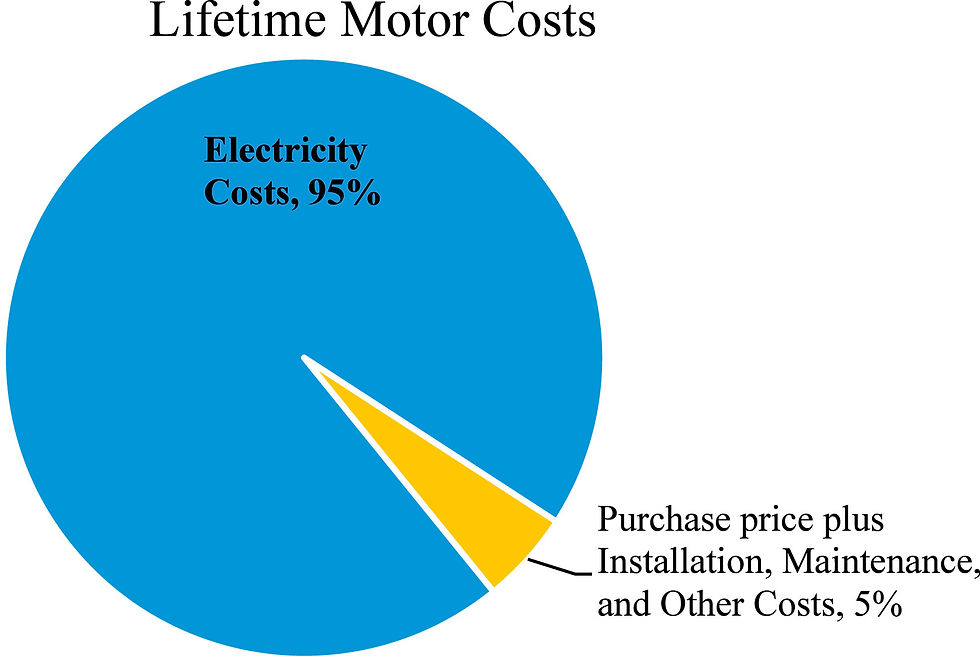
These new technologies are quite capable of identifying additional benefits such as bad lubrication conditions. In this way, they constantly help to reduce the operating costs of a system. This is particularly relevant because 95% of the lifetime costs of a motor are electricity costs alone, and in the case of lubrication condition detection, the subsequent lubrication optimisation is a relevant adjusting screw.
There is a lot of imagination in these topics. It is therefore well worth giving it free rein.
Author: DI. Mag. Markus Loinig
Email: markus@senzoro.com